How to Prolong Useful Life for your CNC Routers
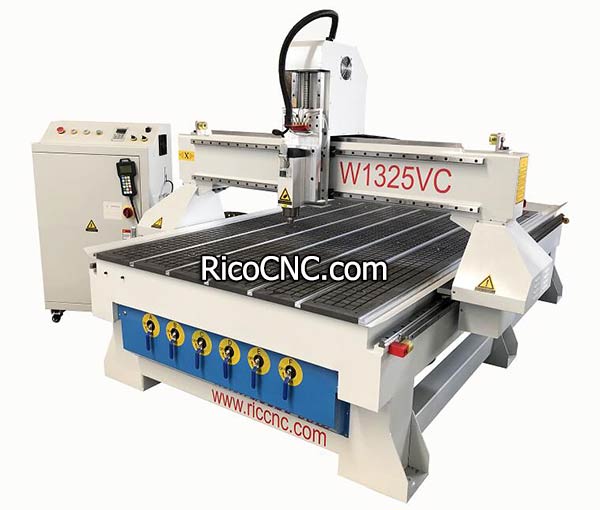
How to Prolong Useful Life for your CNC Routers
Preventive Maintenance for CNC Routers
This article offers guidelines for maintaining a CNC router machine. Well-built CNC routers can potentially operate for many years, but only if they are properly cared for. A disciplined approach to preventive maintenance can extend the useful life of any CNC router, reduce repair costs, and improve cut quality. Most preventive maintenance tasks listed in this article can be performed by the end-user, but there are times when it is important to call the CNC router dealer for help, and those are addressed later in this article.
Proactive Steps to Prolong Useful Life:
Daily Maintenance
The following maintenance tasks should be performed daily:
1. Check the machine’s air pressure regulator
ATC CNC routers with air cylinder, feature an air pressure regulator that helps to control incoming air pressure. On an auto tool change machine, the air pressure regulator is located at either the back of the machine on the right frame rail or in the middle of the right side of the machine’s frame. The regulator should be adjusted so the incoming pressure to the machine is within the manufacturer’s specification (between 0.5 to 0.8 MP for a Rico CNC Router). To adjust the regulator, pull up on the center cap and rotate to set the desired pressure. After pressure is adjusted push down on center cap to lock in place.
2. Purge water and oil separators
ATC routers, feature water and oil separators on the incoming air line. The water and oil separators need to be checked and purged daily to make sure that no contaminates get through the air supply to the machine. To purge the oil and water separators turn the knobs at the bottom of each unit until clean air flows out. Some of these units have red push buttons to purge instead of knobs that turn.
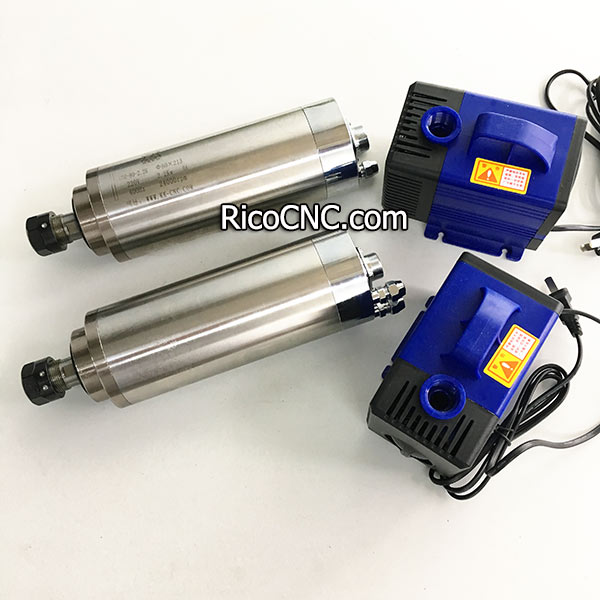
3. Check heat exchanger (if the spindle is liquid-cooled)
The coolant reservoir in the heat exchanger should be checked once or twice a week to make sure that the coolant level is full. If coolant is needed, use a 50/50 mixture of distilled water and ethylene glycol. Always make sure that the heat exchanger is on and running at the start of each day. If the spindle is run for an extended amount of time without cooling it will damage the bearings in the spindle.
4. Clean the spindle fan (if the spindle is air-cooled)
Dust accumulates on the spindle’s cooling fan and can cause it to become out of balance. Use compressed air to blow off the fan daily.
5. Check computer connections
6. Sweep work area
7. Examine tools before cutting
8. Check dust collector bins/bags (if equipped) and empty if needed
Weekly Maintenance
The following maintenance tasks should be performed weekly:
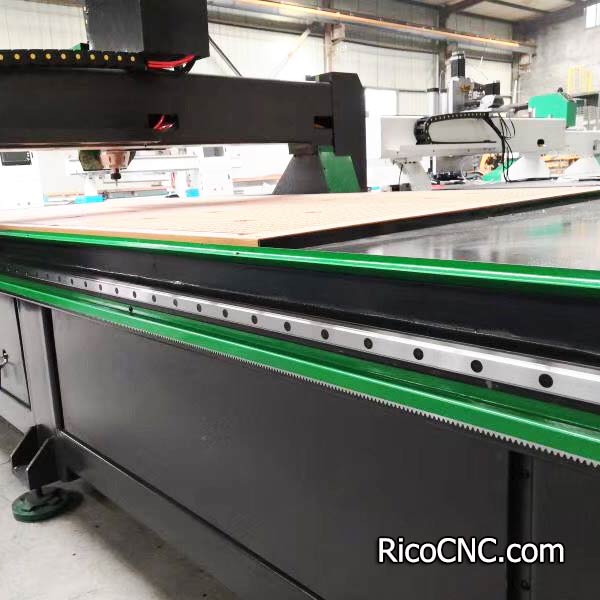
1. Lubricate bearings and screws
CNC routers can use a combination of rack-and-pinion, ball screw, and lead screw devices to create motion. Each of these requires regular lubrication, and end-users should find out from their dealer how many of each of these devices are on the machine and where they are located.
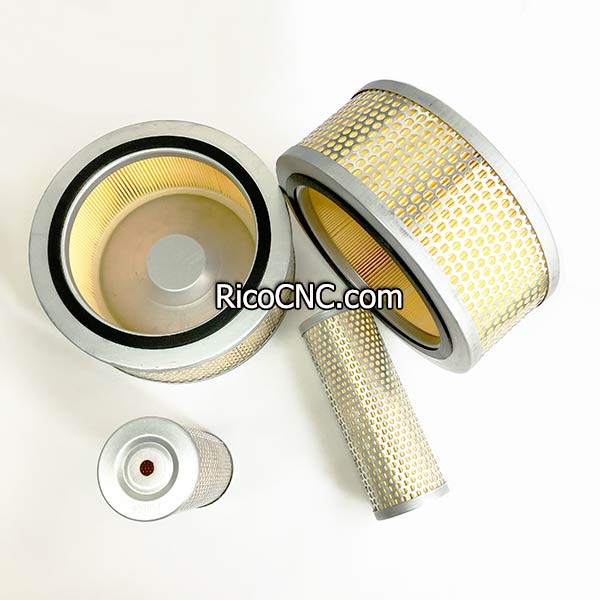
2. Clean vacuum pump filters
Vacuum pump filters should be checked and cleaned each week and replaced when necessary. Take great care when removing and cleaning the filters not to let any debris enter the vacuum pump inlet.
3. Clean air filter in the heat exchanger (if the spindle is liquid-cooled)
The air filter on the heat exchanger should be cleaned with compressed air once a week and replaced as needed.
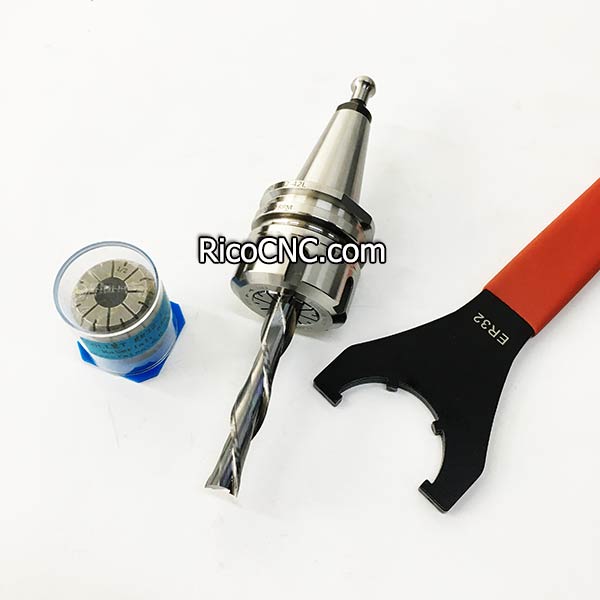
4. Clean tool holders and collets
Tool holders, collets, and collet nuts must be rust-free and clean. Use a mild scotch-bright pad to clean any rust. Apply a very light oil to prevent oxidation, and then remove excess oil with a clean, soft rag. Never use abundant oil or grease. Typically these components need to be cleaned weekly, but frequency really depends on the amount of moisture in the air and how quickly rust develops. Components should look like they are new at all times.
5. Clean the spindle taper
Cleaning the spindle taper should be done once a week. Wipe the taper very well with a green scotch bright pad, use compressed air to blow the taper out, and then wipe with a clean dry cloth.
6. Wipe off excess grease
7. Double-check all connections
Monthly Maintenance
The following maintenance tasks should be performed monthly:
1. Check and change heat exchanger coolant filter
Once a month the heat exchanger coolant filter should be inspected and changed if needed.
2. Lubricate racks
If the machine features any rack-and-pinion devices, the racks should be lubricated monthly. A typical Rico CNC engraving machine has 3 gear racks, 1 on the X-Axis and 2 on the Y-Axis.
3. Check for loose bolts on the machine and tighten as needed
4. Wipe rails with a scotch bright pad
Quarterly Maintenance
The following maintenance tasks should be performed quarterly:
1. Clean or replace relief valve filter on the vacuum pump
2. Change vacuum pump oil, if applicable
3. Change grease cartridges, if applicable
4. Clean rack-and-pinion and re-lubricate
5. Clean overall machine
These are just a few simple steps that will help to maintain the high performance standards inherent in every CNC machine.
RicoCNC focuses on CNC machine trouble-shooting and supplies a range of high quality CNC spare parts and tools. It is necessary to keep some spare parts for your machine, which will help increase your productivity and improve your manufacturing operations when some parts damage. ds inherent in every Rico CNC machine.
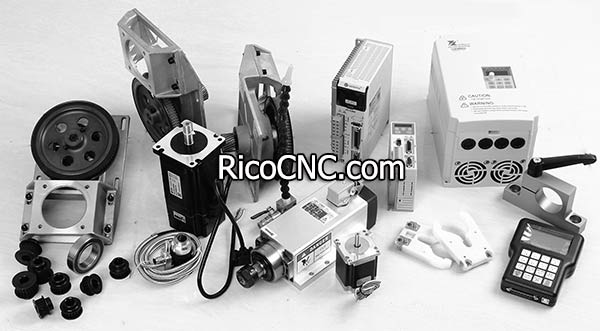